The Utilicor Team is comprised of a group of diversely talented individuals all committed to delivering the highest quality coring equipment, products and services. We strive day in and day out to exceed your company’s expectations. We understand that we are not your only choice when choosing a keyhole equipment and materials supplier, but we endeavour to be your first choice.

Andrew Pollock is a business executive whose well-honed customer-service approach allows the company to effectively understand and address all of the product-oriented requirements of our customers. Andrew co-founded Utilicor in 2012 and has worked in every aspect of the business over the past 18 years. As President and CEO Andrew guides the company in achieving its mission of delivering high-quality, cost-effective products and services to the North American utility maintenance and service marketplace. He also functions as General Manager and is responsible for the on-time production and quality assurance of manufacturing operations. His focus is on product development and improvement programs that will increase the value-added performance of the company’s industry leading coring units and permanent pavement bonding compound, Utilibond™.
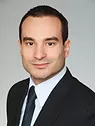
Bogdan Lupu joined Utilicor with 8 years of well-honed financial and business administration skills from the technology sector having worked in both large multinationals such as General Electric and IBM as well as Toronto-based start-ups, where he managed the accounting and finance departments. With working experience in Canada, France and Hungary and with working proficiency in English, Spanish, French and Romanian, Bogdan brings a multinational, cross-cultural perspective to the company. Blended with his experience in the technology sector and his proficiency in multiple accounting software packages, Bogdan is focused on implementing process improvements to increase efficiency and enable the Company to scale up to meet the future needs of our expanding family of customers worldwide.

Pat Colangelo has more than 25 years of experience in a variety of manufacturing, fabrication and assembly operations, including several years of direct experience with the Utilicor product line as Plant Superintendent of the ISO 9001 2000 certified manufacturing facility that supplied Utilicor with many of the fabricated parts and components used in its coring units, before those activities were brought in-house.Technically trained as a Machine Operator and Precision Metal Fabricator, Pat began his career as a sheet metal mechanic with one of North America’s leading manufacturers and suppliers of parts and components for the transportation, construction equipment and heavy machinery industries, and rose through the ranks to become Production Supervisor responsible for production, fabrication and scheduling.In 2008, Pat joined Utilicor Technologies as Production Manager and is responsible for all aspects of sourcing, scheduling, production and quality assurance. His strong commitment to customer service and fast, accurate and high quality work, will help Utilicor maintain its technological leadership in the global market for truck, trailer and skid steer-mounted coring equipment and its reputation for meeting the specialized demands of its customers with innovative solutions that keeps it at the cutting edge of keyhole technology.
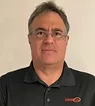
Jeff Haas is a Mechanical Engineering Design Technologist with more than 30 years’ experience in a wide variety of manufacturing environments that includes design and hands-on manufacture from prototypes to finished product. This knowledge extends to encyclopedic operational familiarity with a wide range of manufacturing and production equipment that includes laser and plasma profiling, boring mills, CNC and manual lathes, welding, iron working, shears and punch, brake and drill presses.
By combining “out of the box” design thinking and problem solving with well-honed computer skills that include advanced levels of AutoCad, Solidworks, Visual Manufacturing, QuickBooks and other ERP software, Jeff brings together an arsenal of design, manufacturing and business assets to arrive at the most practical and cost-effective solution that will help Utilicor maintain its technological leadership in the global market for truck, trailer, skid steer-mounted and self-propelled coring equipment.
And unlike many designers Jeff can, and often does, follow his designs into production and manufacture with a full set of production scheduling, urchasing and quality assurance skills to ensure that those designs meet all of the requirements and expectations of the customer and the manufacturer.
Combined with a “can-do” attitude, these skills and experience, and years of customer contact for sales issues, order entry, quotations and product specification will help the Company ensure that industry and customer requirements are met by engineering specifications and manufacturing quality that enhance its reputation for meeting the specialized demands of its customers with innovative solutions that keeps it at the cutting edge of keyhole technology.
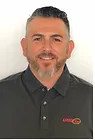
Jody Robles joined Utilicor Technologies in 2018 from Southwest Gas a local gas distribution company with operations in Arizona, Nevada and California, where during 17-years of service he rose to become the resident expert on keyhole coring and reinstatement technology and established it, along with vacuum excavation, as the approved and preferred method of performing and repairing pavement utility cuts throughout the company’s service area. Jody is proficient in all aspects of gas service operations making use of the keyhole coring process including: cathodic protection, distribution pipe and service replacement using HDD and Split & Pull, and the connection and abandonment of services on moratorium roadways.
As Manager of Field Operations, Jody is also responsible for trouble shooting, problem solving and process training with contractors, local municipalities, transportation and other agencies and utilities.
As our “agent of change”, Jody is our “how-to-guy” in the field, and our eyes and ears to issues that will help maintain our technological and performance leadership and keep Utilicor at the “cutting edge of keyhole technology.”
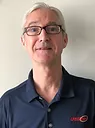
Michael brings 30 years of customer relations experience and well honed sales, coaching and project management skills to Utilicor. He has worked with companies such as Xerox, Unitel Communications and Eagle’s Flight Creative Training Excellence. Michael facilitates our sales process by coordinating internal and external efforts to ensure that they meet the needs of our customer. Recognizing that good communications are essential to successful outcomes, Michael contributes to smooth execution in all areas to help us achieve the most positive experience possible for each and every one of our customers.
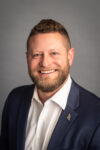
Nik Taylor is starting his 8th year in the underground construction industry as Utilicor Technologies Inc. Manager of Business Development. Nik started his career in underground construction with HammerHead Trenchless and Subsite Electronics. His professional career began as an Art Director at a Newspaper in San Diego County and worked in marketing and project management in electrical sign construction before joining the underground construction industry.
Nik currently serves as the Treasurer of the Board for the NASTT South Central Chapter. Nik has worked with the Ditch Witch dealer channel, assisted damage prevention associations, and has helped develop training and best practices for large organizations.

Subject Matter Expert
Ryan Singh has been with Utilicor for over a decade and has had a hand in designing, wiring and plumbing every Utilicor unit on the market. Overseeing the Utilicor hydraulics team, his decades of technical hydraulics experience make him our premier resource when customers need to troubleshoot Utilicor units.